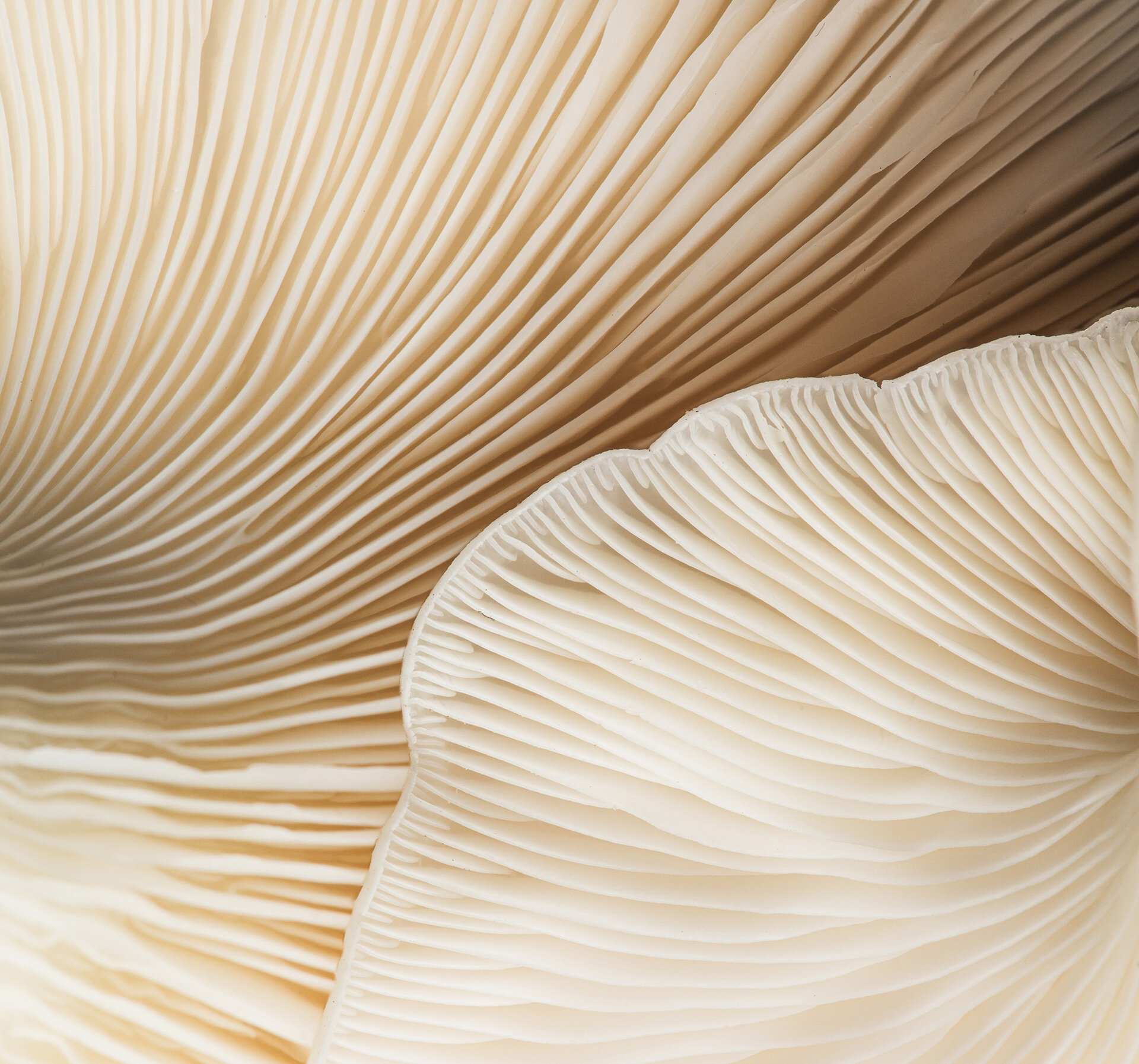
Projects
Servo-Driven Animatronic Bird – Inspired by the Enchanted Tiki Room
Personal Engineering Project | In Progress
Ahh, the Tiki Room — a longtime favorite attraction of mine at Disney (very underrated, in my opinion!). My family has a particularly fond story from when I was younger. I remember seeing the Tiki Room walking into Adventureland. I always wanted to know what it was about (the promise of tikis and lit torches never hurt either!).
Anyway, I kept asking my family if we could try out the Tiki Room. To which they would always say, “No!” Eventually, later in the day — hot, sweaty, and tired — they finally relented under my pressure, and we went into the Tiki Room.
What happened took all of us by surprise. The whole room came to life — the song, the birds, the plants, the tikis... even the walls! My dad couldn’t stop laughing. We were all just in amazement.
To this day, I always make time to visit the Tiki Room. It’s an incredible piece of show engineering from Disney. And from a purely mechanical engineering standpoint, it’s stunning. So I decided that, as a personal engineering project, I would build my own Tiki Room–inspired parrot, based on José — both to demonstrate and expand my engineering skills.
Current Challenges & What’s Next
This project is still in active development, with several key components under evaluation:
Servo Selection & Finalization(Now Finalized):
Four digital servos were selected to handle a range of force and motion requirements across the animatronic subsystems:
AGFRC A20CLS(x2): Chosen for tilt actuation and head turning, offering a compact aluminum case, programmable response curve, and high-voltage digital performance suitable for fast directional changes under moderate load.
AGFRC A80BHSW: Selected for the body rotation mechanism due to its 36 kg high torque rating, brushless motor, and IP67 waterproofing. Its holding strength ensures smooth, stall-resistant rotation for the central structure.
KST X08 (×2): Lightweight and ultra-slim, these digital servos were selected for beak actuation and chest movement, providing quiet motion, precise response, and low-profile integration in tight spaces.
Bracket Clamp & Hinge Redesign: The current custom-designed hinge and bracket clamp for the gimbal assembly (mounted around the rotating shaft) have proven costly and complex to fabricate, especially when I’m limited by the makerspace that is available to me in regards to the tools I can use. I’m now evaluating off-the-shelf alternatives that offer the same functionality while reducing cost and improving assembly simplicity.
Body Rotation Mechanism: A vertical shaft driven by the A80BHSW is now integrated with custom bushings and a rotating collar. Design balances structural load using offset placement and a future torsion spring counterweight, allowing for realistic tilt-back body motion around anchored steel legs.
Chest Movement for Breathing Effect: The chest "breathing" feature is being prototyped using one of the KST X08s, mounted beneath the chest panel to produce a subtle outward pulse. Mechanical clearance and mounting geometry are in development.
These next steps focus on refining motion quality, structural simplicity, and production feasibility — while staying true to the character-driven performance of Disney’s original Audio-Animatronics.
Engineering Skills Demonstrated So Far
• Multi-axis motion design | • Bracket and hinge evaluation for rotating assemblies |
• GD&T in NX | • Servo load analysis |
• Tolerance stack-up planning | • Siemens NX modeling |
• DFM principles | • Creative problem-solving |
• Servo selection and torque balancing | • Custom clamp and collar design |
• Motion linkage design (clevis, push/pull) | • Component integration planning (A20CLS, A80BHSW, KST X08) |
Project Stage & Technical Summary
This project is now entering the early manufacturing phase, following completion of all major mechanical design work. Full 3D CAD assemblies have been finalized or are being finalized in Siemens NX, with multiple subsystems — including swivel, tilt, body rotation, beak actuation, and breathing motion — now servo-selected and structurally integrated.
Initial fabrication is underway using 6061-T6 aluminum stock, combining waterjet-cut panels with custom brackets and precision-bored motion components. Servo integration will follow immediately, with performance tuning, motion calibration, and spring-assist balancing next on the roadmap.
Inspiration reference: José from Disney’s Enchanted Tiki Room. This project is a personal engineering build and is not affiliated with or endorsed by The Walt Disney Company.
This personal project explores multi-axis motion control for an animatronic bird. Using Siemens NX, I developed a servo-driven mechanical system featuring:
A rotating shaft for head swivel
A stacked tilt mechanism actuated via linkage
A servo-embedded beak movement system
The design uses Sonic Hubs and flanged bearings to suspend the gimbal assembly and is constructed from 6061-T6 aluminum for strength and machinability. Ongoing development includes:
Servo selection and power balancing
Clamp hinge integration for head tilt
Tolerance stack-up planning for mechanical clearance
Final linkage and actuation tuning for smoother, lifelike motion
This bird is being designed with real-world design-for-manufacturability (DFM) principles and serves as a themed entertainment prototype that demonstrates mechanical complexity, servo integration, and motion synchronization.
University Keystone Senior Design Project
This Project was done in the years 2020-2021 as a keystone project for Saint Martins University. The Project was to design a device that was ergonomic and facilitated the ability to girdle trees in an efficient manner on tree farms for the Washington State Department of Natural Resources. For this design engineering codes ISO/PAS 45005:2020, ANSI/ASME Y14.1, ANSI/AGMA 2003-B97 were used.
Tree Girdler Prototype
Calculated Stress on Gears designed
Deformation from Calculated Stress
This Project was a great experience from a design concept to a working prototype. The added difficulty of this project was that it was done in the middle of a pandemic, and therefore funding for this project was limited to only $500 dollars since the Washington State Natural Resources budget was low due to cuts, so the team was very limited in what we could do and had to budget well for this project. My team was very successful in coming up with creative solutions to problems. One particularly nasty problem was the challenge of having to drill a square hole! We contemplated casting a part or having a part machined to solve the problem, but both proved to be too expensive so we ended up drilling a 4 mm hole and filed out the corners to make a square hole. By utilizing these solutions the team was able to keep the design under budget and had a surplus of $164.91 after the completion of the project.
This was a team effort, as such, I had various responsibilities and sections that I worked on:
Designed the bevel gears to match a specified set of safety factors
Was one of the designers and modeled the design in AutoDesk Inventor
Gave the original idea for the design as well as designed and 3-D printed out the blade guard
Performed stress and deformation analysis on the prototype
Helped to manufacture and put together a successful working prototype
As the team secretary, I was responsible for scheduling team meetings and directed communication within the team as well as creating a schedule for different phases of the project
We were so successful at our scheduling that we were the first team to complete our prototype in the manufacturing stage whereas other teams had to work up to the last minute to fine-tune their designs and in some cases weren’t able to finish their projects
Personally wrote over 65 pages of the prototype report
AUTOCAD INVENTOR School WORK
This section is a focused look at some work and assignments that I worked on throughout my academic career using Inventor
Lightsaber Hilt Assembly
Lightsaber Hilt
This was my final project in my Inventor class. Initially, the requirements were to replicate a wine opener or to take a manufactured product that consisted of three pieces. Being the type of person that looks for a challenge, I decided to do a manufactured product in order to test my skills. I love Star Wars so I decided to measure and model a lightsaber hilt that I have! Criteria for this project included
Parametric Relations
Fully Constrained Sketches
Geometric Constraints
Minimum features of:
Two Revolved Features
Two Circular Pattern Features
One Mirror Feature
One Fillet
One Offset Feature
One Loft Feature
One Spiral Feature
Title Features
Three views per drawing and including one section view and one auxiliary view
If you click the button below, you will be taken to a viewer where you can see and rotate the lightsaber hilt as well as see an exploded view with all of the different parts.
Hilt Auxiliary View
This is a drawing of the hilt showing the measurements used in mm
Assignments
Here is a video showcasing a homework problem utilizing different constraint features in order for the assembly to work together based on the movement of one part. I loved doing this assignment since I love animation, and while it’s very simple and slow, it represents two parts interacting with constraints based on physics.
Tolerances and GD&T
I decided to pick a drawing showing the use of tolerances and for this assignment, GD&T calculations were required when determining the dimensions
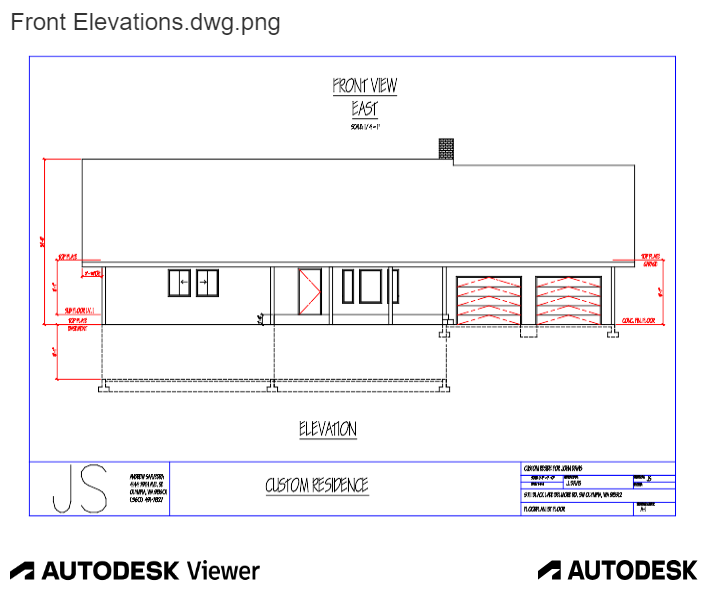
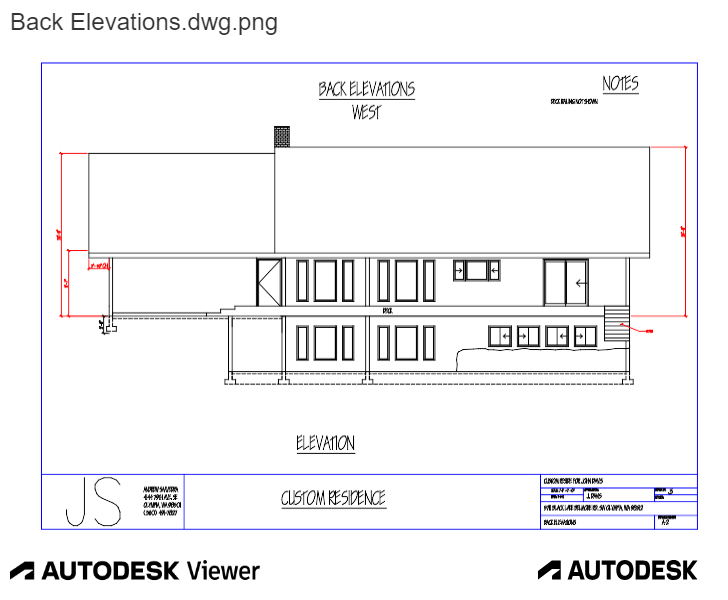
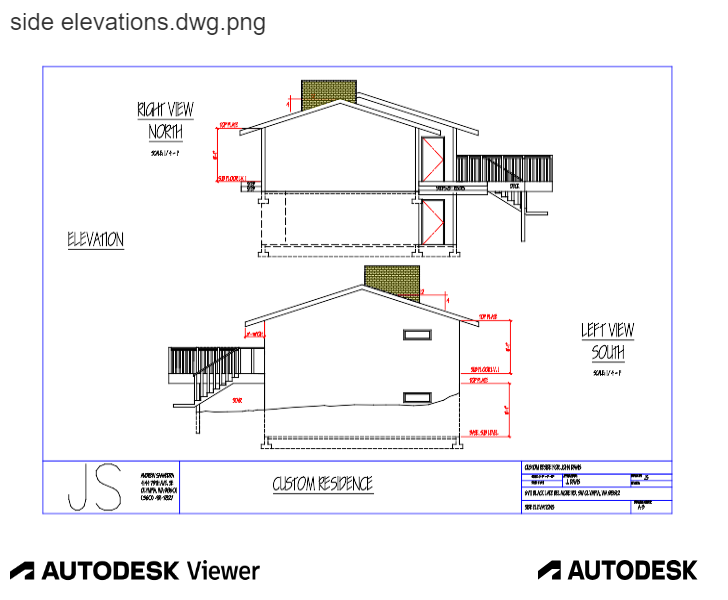
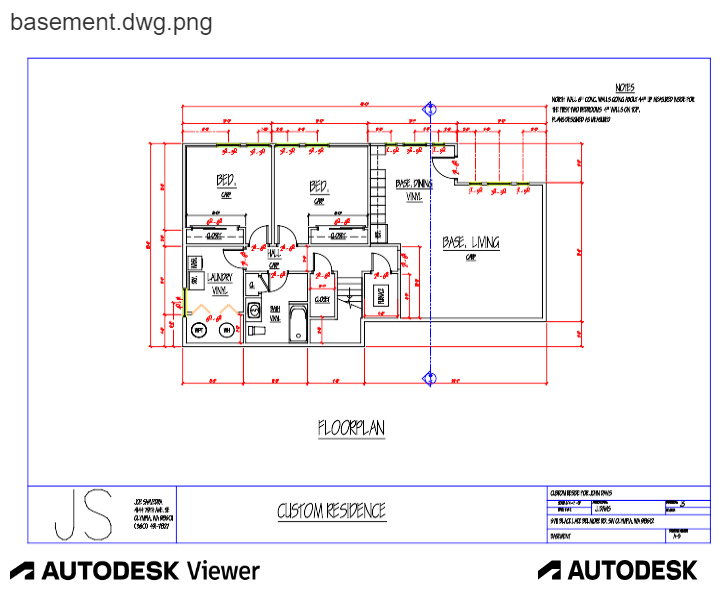
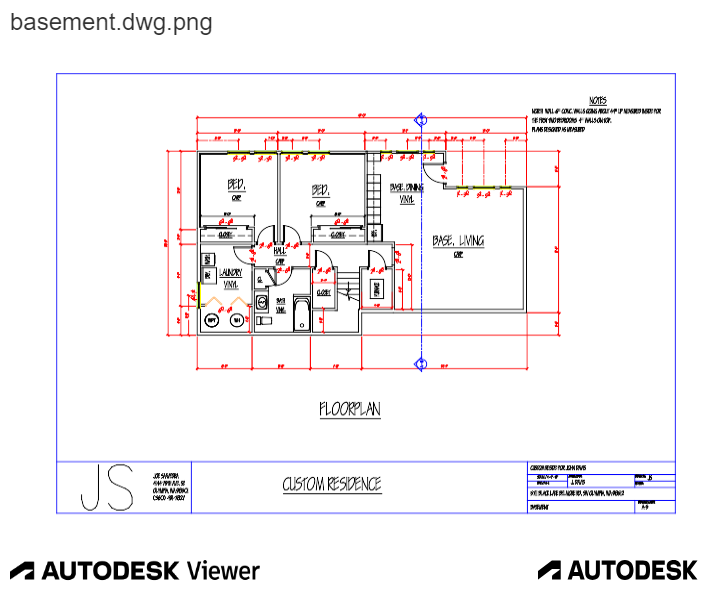
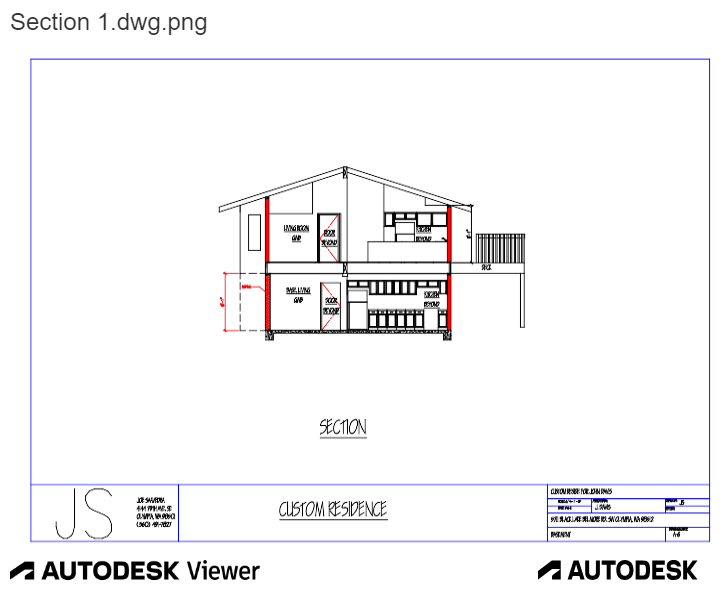
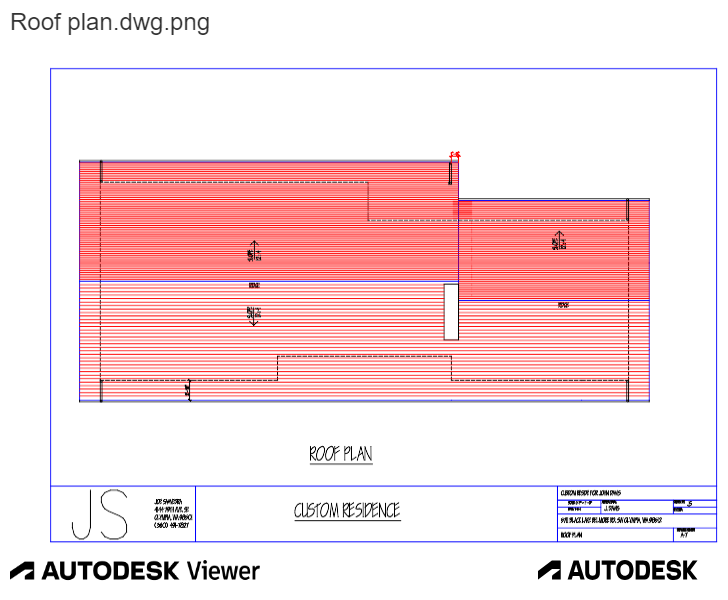
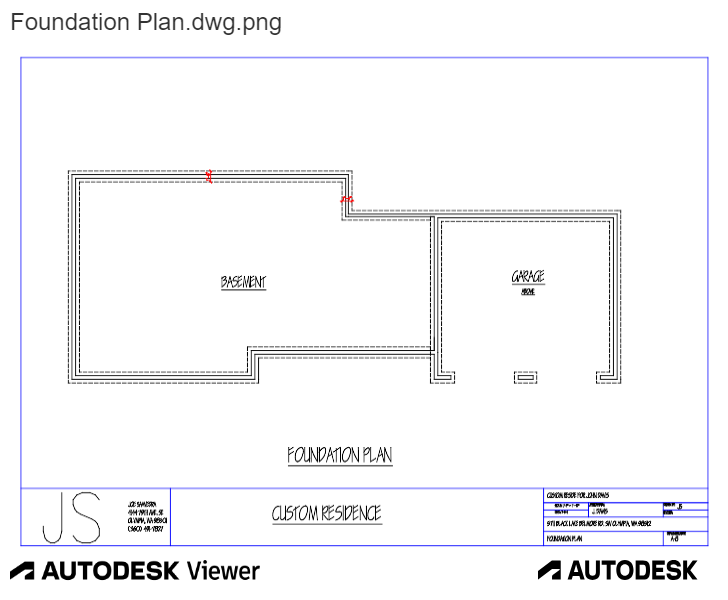
Artwork and Photography
Here I wanted to showcase some of my artwork pieces. You might ask yourself why would I include this in my portfolio, however, I wanted to show my creative side that I think highly contributes to any work that I might do.
The first picture is an experimentation with the common two-thirds rule, where an object is placed off-center in order to make a piece more interesting. In this case, the outside hedge fulfills this purpose. This piece started with basic shapes, then shading, and finally filling out the details. I also just love the nature aspect of the manmade features of the hedge. Not only that but the simple gray and shading remind me of growing up in Washington where the predominant color 9 months of the year is grey tones or almost in a world slightly asleep.
In the second piece I wanted to show some of the processes of making a piece, in this case using geometrical shapes to make something that was pleasing to the eye. I loved working on this piece because it gave me the sense of looking through a kaleidoscope with the ever changing scenes of geometrical shapes.

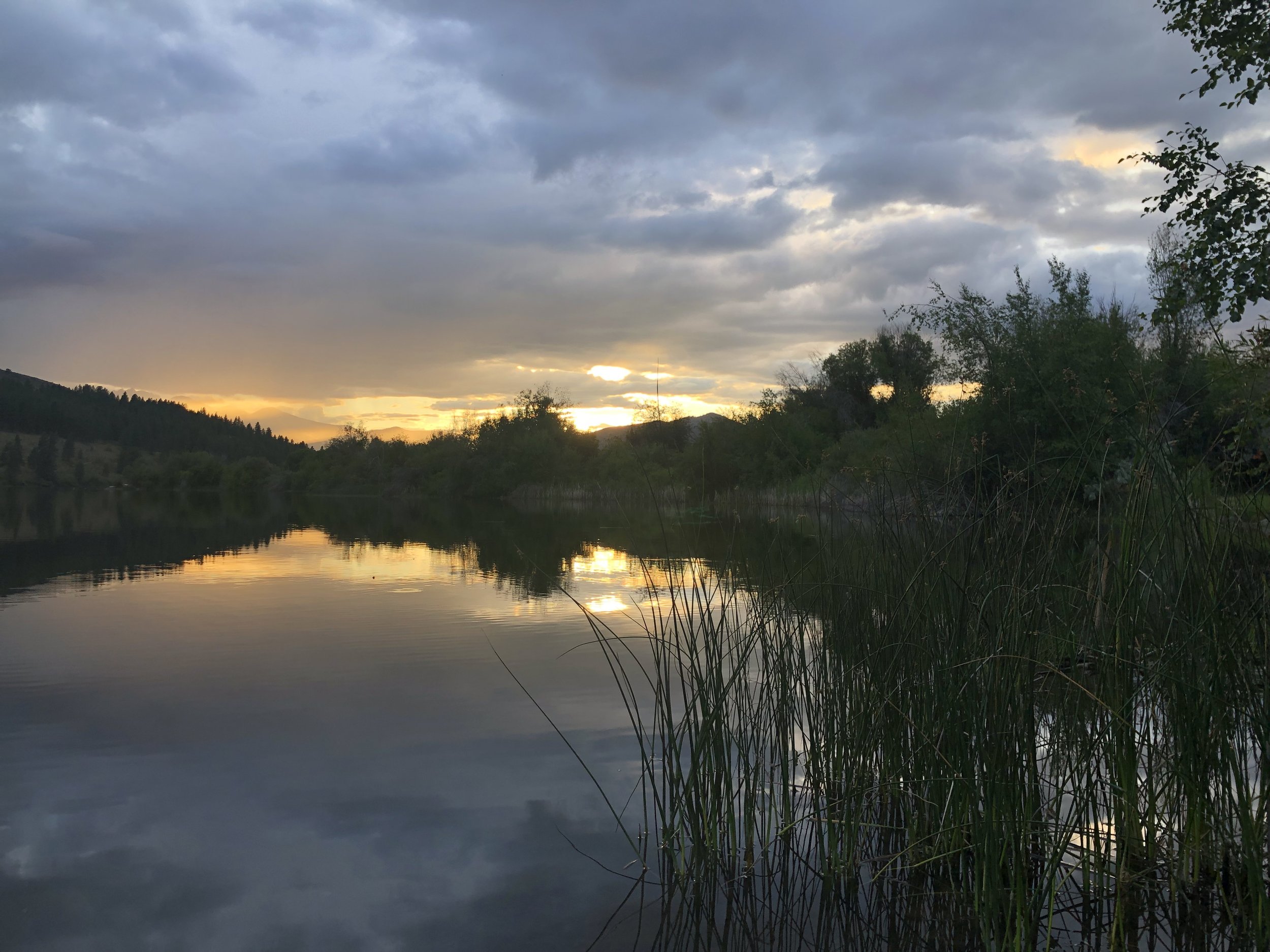
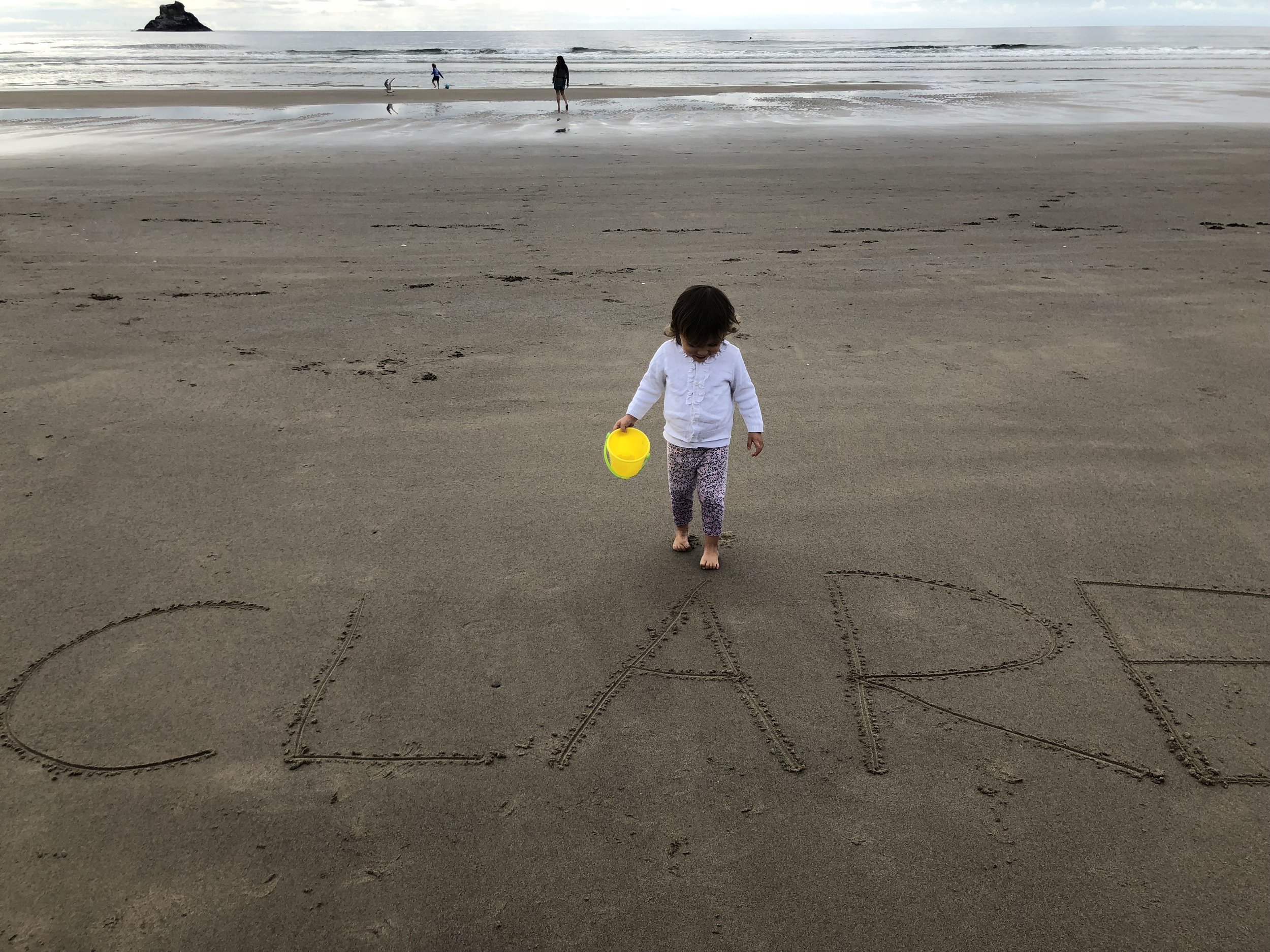
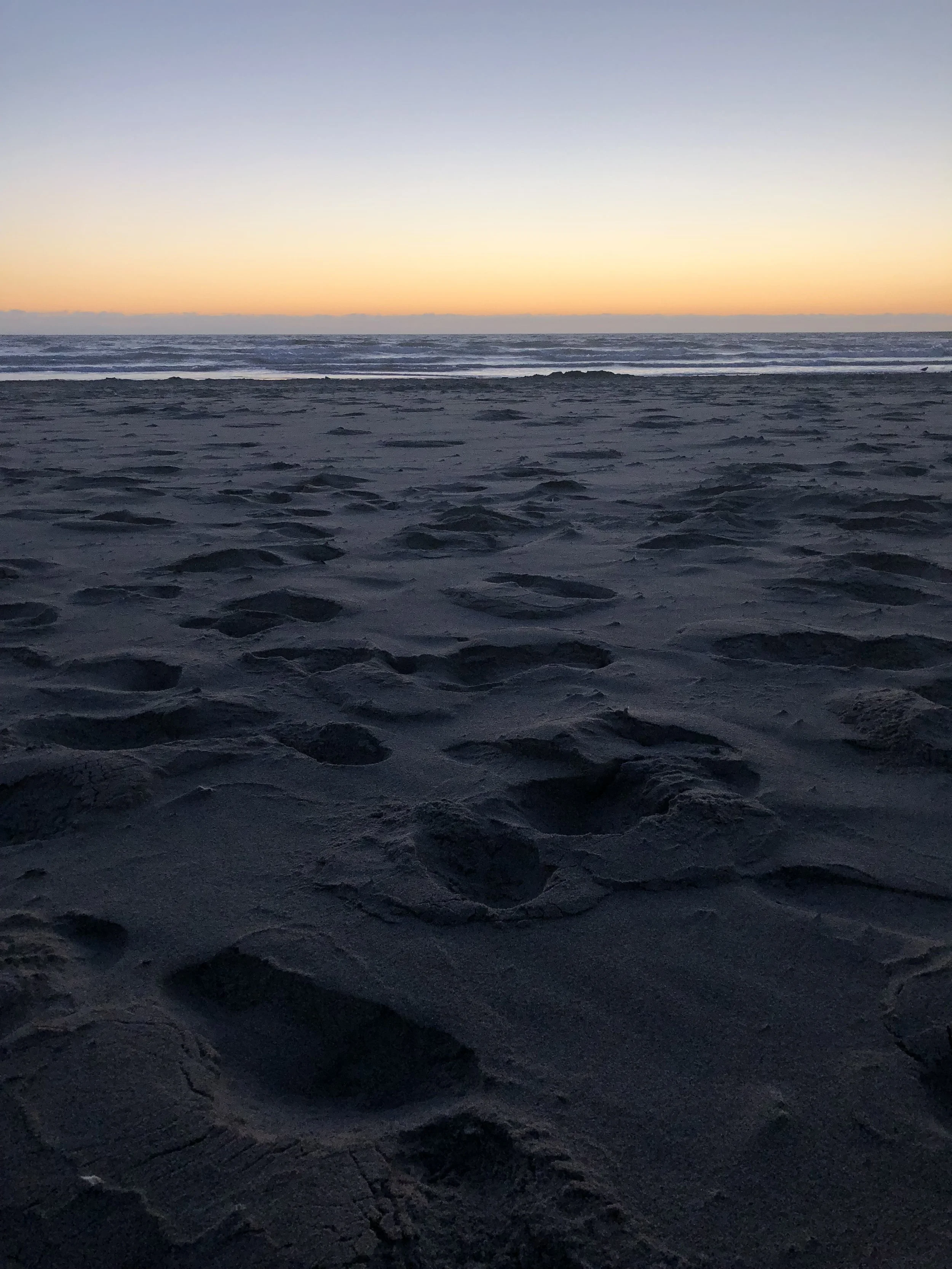
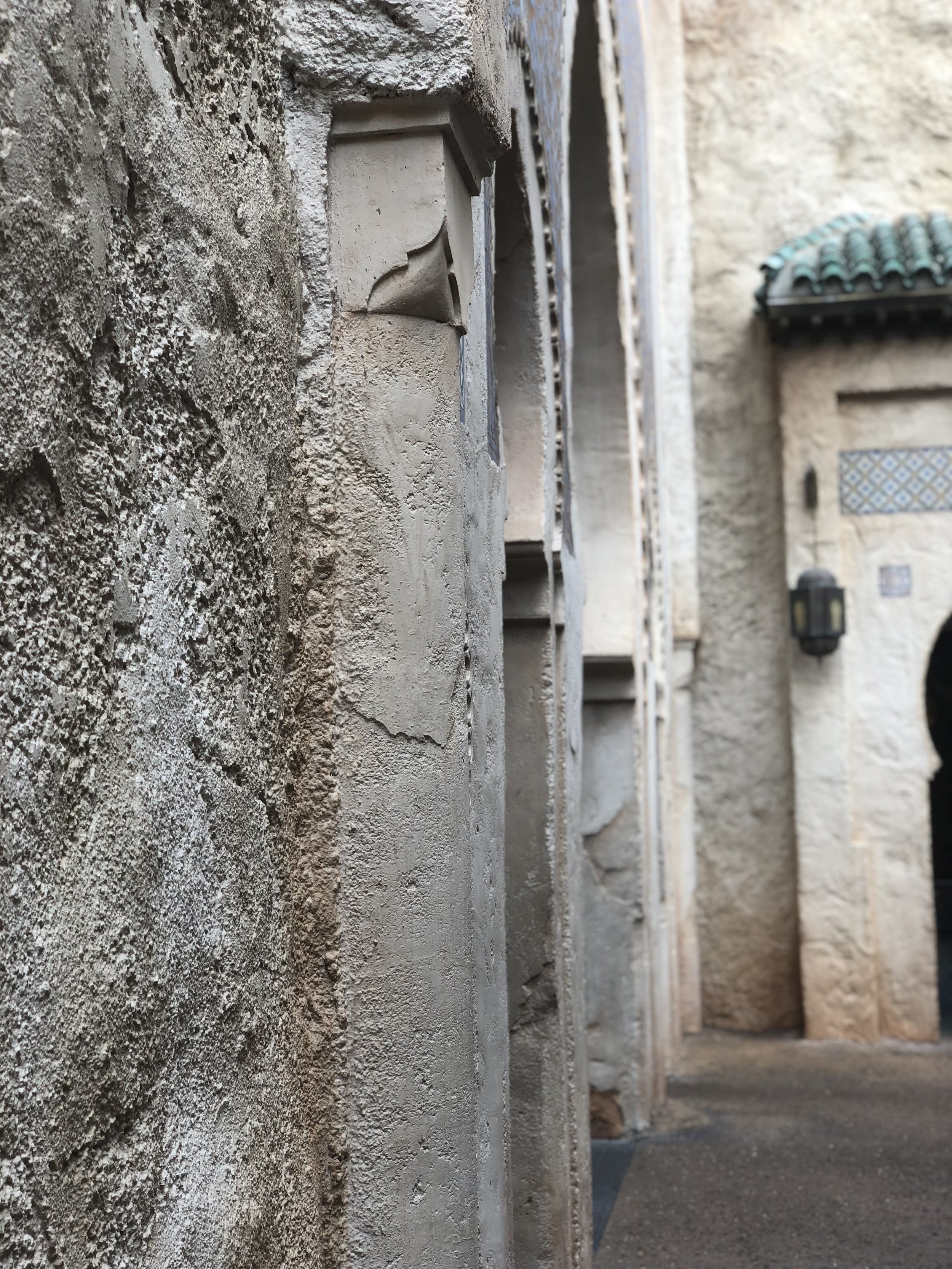
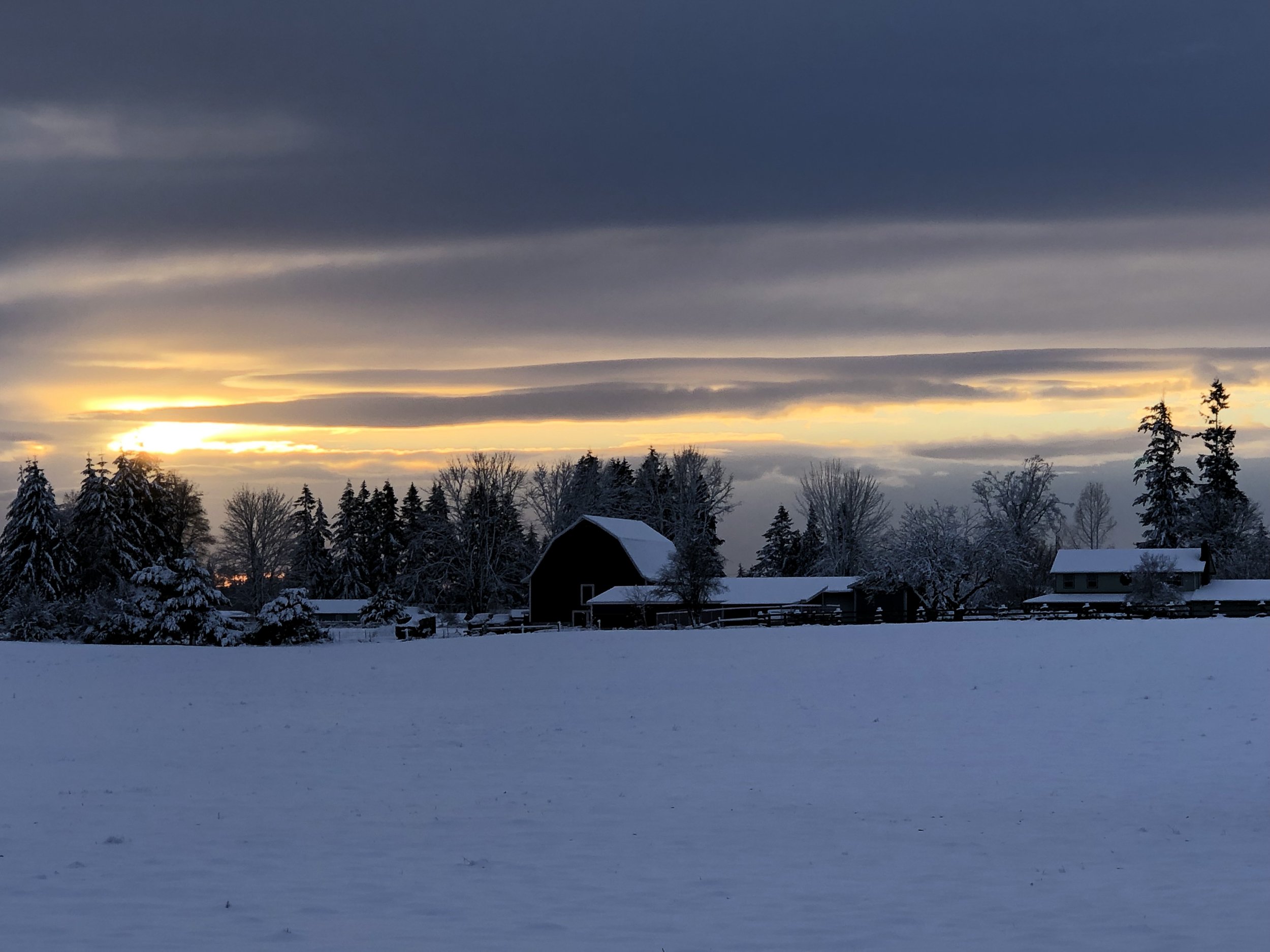